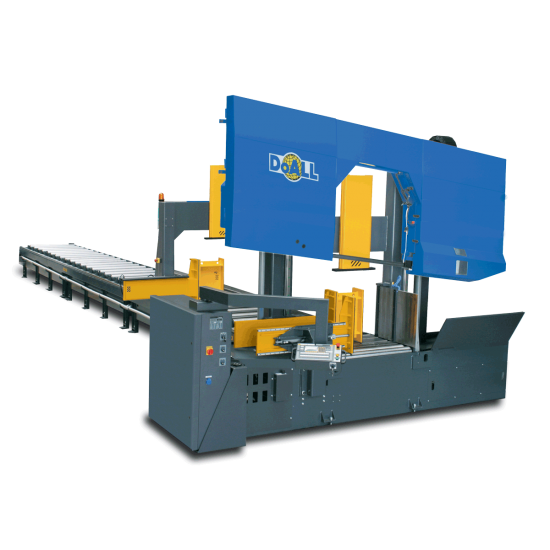
Call For Pricing
DOALL TDC-1000CNC 38" X 40" OLYMPIA SERIES SEMI-AUTOMATIC HORIZONTAL DUAL COLUMN CNC TUBE AND PIPE METAL CUTTING BAND SAW
- Stock: In Stock
- Model: TDC-1000CNC
- Weight: 20,944.00lb
- Dimensions:
- 284.00in x 169.00in x 117.00in
- SKU: TDC-1000CNC
|
|
|
|